ESD Basic: Impatti ESD nei processi produttivi
Abstract
Le aree EPA ed i sistemi di protezione ESD necessano di attività costanti di manutenzione e verifica. Oltre a controlli periodici su dotazione è fondamentale l’ esecuzione di analisi della affidabilità dei sistemi in uso ed il controllo dei materiali utilizzati per la pulizia ordinaria. È altresì importante la scelta di sistemi di protezione “robusti ed affidabili” unitamente alla formazione ed alla certificazione di tutto il personale avente accesso all’ EPA..
La progettazione di aree EPA è una delle fasi più importanti per poter assicurare la protezione da eventi ESD; l’ utilizzo di materiali idonei infatti garantisce l’ efficienza dei sistemi di protezione utilizzati sia nelle condizioni maggiormente critiche (RH 12%) che attraverso il tempo (in questo caso il “design robusto” prevede l’ impiego di prodotti che mantengano le loro caratteristiche per tutta la loro vita – tempo di utilizzo).
Focalizzando l’ attenzione verso le EPA progettate per applicazioni elettroniche il fenomeno ESD diviene particolarmente critico nelle fasi di maneggiamento “handling” e movimentazione ed in questo caso il criterio di base da adottare e’ quello di dimensionare i sistemi di protezione per poter proteggere i componenti maggiormente sensibili (classe ZERO – vedi tabella a).
# | Class | Voltage Range |
---|---|---|
1 | 0 | < 250 |
2 | 1A | 250 to < 500 |
3 | 1B | 500 to < 1000 |
4 | 1C | 1000 to < 2000 |
5 | 2 | 2000 to < 4000 |
6 | 3A | 4000 to < 8000 |
7 | 3B | > or = 8000 |
Tab a) - HBM ESDS Component Classification REF EOS/ESD STM 5.1 – 1998
Le soglie di sensibilità dei componenti ESD sensitive vengono stabilite in base al modello HBM (Human body model - 100 pF – 1500 ohm) e per poter garantire l’ affidabilità di un EPA (ESD Protected area) per applicazioni elettroniche sono decisamente utili alcune normative di sistema quali :
- IEC 61340-5-1
- ANSI S.20.20
- CEI 101-1 (Guida)
Tali documentazioni infatti definiscono le caratteristiche dei sistemi di protezione da impiegare (limiti – proprietà) i quali sono dimensionati per poter garantire 100 volt quale massimo potenziale ammesso in zone ove si maneggiano ESDs non protetti (ref. HBM “Human Body Model”). Ne consegue quindi che il personale sia l’ elemento più importante in quanto può influenzare l’ affidabilità di un processo ESD sia in sede di progettazione, di esecuzione e di mantenimento.
Una analisi superficiale di questo criterio ha indotto molte aziende e/o realtà produttive ad indirizzare i maggiori sforzi verso il l personale operativo “diretti”; quanto sopra invece può essere considerato un grosso errore poichè il raggiungimento dell’ obiettivo: max 100 HBV in tutti i punti ove gli ESDS sono maneggiati direttamente, è determinato dal fatto che tutto il personale ne sia a conoscenza ed in grado di favorire il raggiungimento dello stesso e che le aree EPA possano agevolare tale obiettivo (progettazione – apparecchiature - design). A tal proposito sono elencate le aree/mansioni direttamente coinvolte nella gestione e nella applicazione di un programma ESD:
- Progettisti
- Laboratori
- Managers
- Responsabili qualità – ESD Coordinator
- Responsabili formazione
- Manutentori - addetti alle pulizie
- Personale a diretto contatto con ESD sensitive (linea produzione – magazzino)
La progettazione e la verifica in laboratorio sono fasi decisamente importanti e quindi la definizione dei parametri e la simulazione e la verifica in laboratorio sono elementi fondamentali per garantire l’ affidabilità di una EPA.
Questi elementi possono incidere in maniera determinate sul mantenimento di una area EPA quasi eclusivamente nel’ ambito della scelta delle soluzioni; di fatto sono attività antecedenti alla attivazione della stessa e quindi pur influenzandole possono essere considerate periferiche a quelle di manutenzione/monitoraggio/routine.
Per non compromettere l’affidabilità nel tempo in un processo produttivo hanno un ruolo maggiore:
1. I managers : Essi possono influenzare in maniera determinante il comportamento all’ interno di un area EPA attraverso esempio e disciplina.
2. I responsabili qualità ed il coordinatore ESD : Gli obiettivi principali dei responsabili qualità e ESD sono quelli di produrre e diffondere il programma ESD locale e di garantire l’ affidabilità delle EPA attraverso verifiche periodiche.
3. I responsabili formazione : La formazione e la certificazione degli operatori sono un elemento fondamentale poichè tutto ilpersonale avente accesso all’ EPA “inclusi visitatori, addetti alle pulizie” deve necessariamente conoscere le regole di base su cosa può fare e su cosa non deve fare in presenza di ESD sensitive components.
4. I manutentori ed addetti alle pulizie : l’ impiego di prodotti non idonei o le mancate verifiche funzionali possono alterare anche in maniera definitiva le proprietà antistatiche di alcuni sistemi di protezione e a tal proposito si mostrano in grafico 1 le curve di HBV relative ad un pavimento statico dissipativo trattato con cera ESD ed in grafico 2 le curve di HBV dello stesso pavimento trattato superficialmente con un prodotto non idoneo per applicazioni EPA.
5. I personale operativo : attraverso operazioni improprie e mancato rispetto delle procedure gli utilizzatori di EPA e sistemi di protezione possono alterare l’ equipotenziale all’ interno delle aree protette da ESD introducendo potenziali e campi elettrostatici non desiderati.
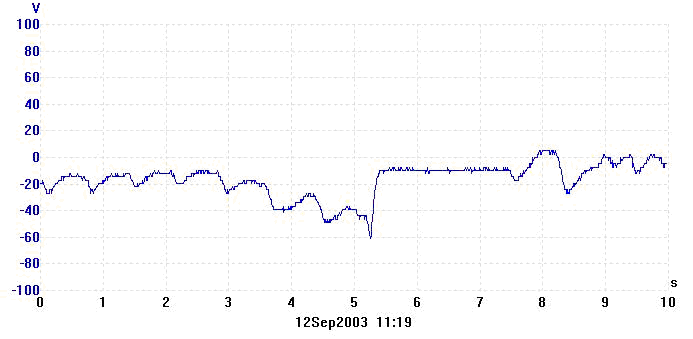
Grafico 1 - Pavimento statico dissipativo trattato con cera ESD al 40%RH
Tutti gli elementi negativi sopraelencati ed eventuali altri contributori che indipendentemente dalla loro natura possono influenzare pesantemente l’ affidabilità di un processo produttivo possono essere condensati in un concetto molto noto e diffuso tra gli addetti ai lavori: errore umano.
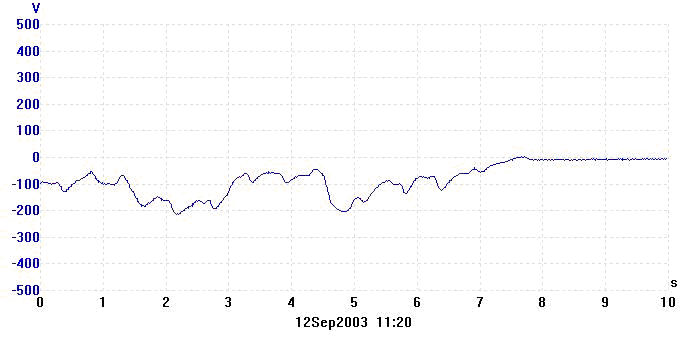
Grafico 2 - Pavimento statico dissipativo trattato erroneamente con cera comune al 40% RH
In ambito ESD l’ errore umano può essere eliminato/minimizzato attraverso la scelta di soluzioni robuste e può essere gestito/minimizzato attraverso attività di mantenimento/formazione (programma ESD - Maintenance).
In entrambi i casi si possono ottenere buoni risultati ed in entrambi i casi si avranno costi iniziali ed opportuni ritorni sull’investimento.
Focalizzado l’ attenzione sull’ HBV (Human Body Voltage) in quanto il suo controllo è l’ obbiettivo principale delle normative vigenti si citano alcuni esempi di messa a terra del personale e relativi benefici.
Personale sitting: il personale che opera in postazione sitting per poter garantire la soglia massima di HBV deve necessariamente indossare il bracciale anche se già indossa calzature ESD. I limiti di questo sistema e principali problemi riscontrati durante le verifiche ispettive sono:
- Controlli giornalieri mancanti – intermittenti
- Bracciale non collegato
- Cinturino lasco
- Cavo danneggiato
- RG > 35 mohm
- Possibilità di “fail “ tra un controllo e l’ altro (daily basis)
Questi inconvenienti possono essere completamente eliminati attraverso l’ uso di centraline con monitoraggio continuo che consentono di verificare costantemente l’ affidabilità della messa a terra del sistema operatore/bracciale “user level” e superficie di Lavoro.
In questo caso i costi iniziali sono maggiori ma scompaiono definitivamente i costi di gestione (controlli – archiviazioni - verifiche) con vantaggi consistenti in termini economici nel giro di pochi mesi.
Un altro elemento che può innescare problemi di HBV è quello legato alla compatibilità pavimento/calzatura su personale standing e conseguentemente una calzatura impropria può alterare l’ efficacia della pavimentazione in uso.
Molte società optano per l’ impiego di puntali e talloniere per la messa a terra del personale che opera in piedi, tali sistemi potrebbero garantire buoni risultati su pavimentazioni omogenee mentre sono inefficaci a basse umidità su pavimenti non omogenei. Di seguito sono allegati i grafici relativi a “walking test – HBV” sulla stessa pavimentazione mediante l’ impiego di scarpe ESD safe e calzari.
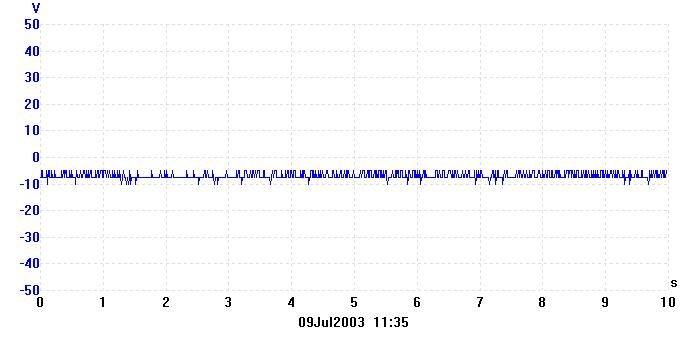
Grafico 3 - HBV su personale con scarpa ESD al 50% RH
Dalle analisi si evince che il personale che utilizza calzari, anche al 50% di RH (vedi grafico 4) eccede i limiti di HBV consentiti ma soprattutto si evince che spesso le misure di resistenza non consentono di valutare completamente le performance in applicazione.
In relazione ai calzari sono elencati principali problemi riscontrati durante le verifiche ispettive:
- Controlli giornalieri mancanti – intermittenti
- Calzare non collegato durante l’ uso
- Fettuccia staccata
- Controllo effettivo di un solo piede (piattaforma unica)
- RG > 35 mohm
- Possibilità di fail tra un controllo e l’ altro (daily basis)
Questi inconvenienti possono essere completamente eliminati attraverso l’ uso di scarpe ESD che di fatto possono avere un costo maggiore ma non necessitano di monitoraggio continuo, non si alterano durante l’ uso , non introducono problemi ergonomici e garantiscono costantemente l’ affidabilità della messa a terra del sistema pavimento/calzatura mantenendo i valori di HBV < 100 volt anche alle basse umidità
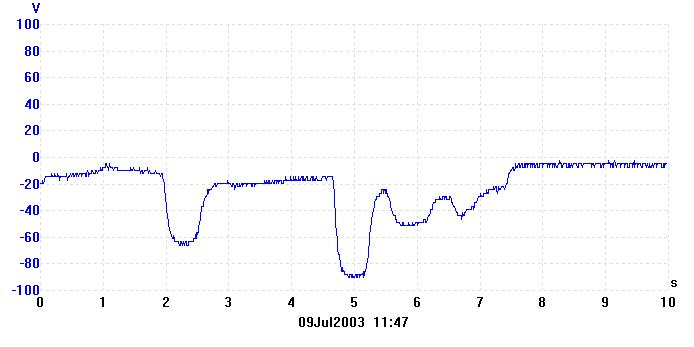
Grafico 4 – HBV su personale con calzari ESD al 50% RH
Anche in questo caso i costi iniziali sono maggiori ma scompaiono definitivamente i costi di gestione (controlli – archiviazioni-verifiche-handling) con vantaggi consistenti in termini economici nel giro di pochi mesi. Da considerare che come nel caso di “unita’ di controllo continuo dei bracciali” diminuisce anche la possibilità di introdurre difetti ESD sulle parti movimentate in EPA. Si allegano le foto 2 e 3 con esempi di calzari e calzature ESD ove si evince anche l’ affidabilità del contatto piede sistema di messa a terra.
Nell’ ambito di questa memoria, l’ attenzione è stata rivolta a due dei sistemi in uso più comuni ma di fatto il “design robusto” dovrà essere considerato per tutti i sistemi passivi e per i sistemi attivi (apparati ionizzanti).
L’ efficacia dei sistemi di protezione invece dovrà essere attivata attraverso piani di mantenimento i cui gli elementi principali possono essere considerati:
- Monitoraggio
- Verifiche ispettive / gestione azioni correttive
- Manutenzione
Questi elementi sono anche richiamati nelle principali normative di sistema tra le quali quelle a cui viene fatto maggior riferimento sono:
CEI EN 61340-5-1
CEO 101-1 Guida
ANSI EOS/ESD S20.20
In particolare la normativa IEC 61340-5-1 viene principalmente utilizzata in paesi della Comunità Europea mentre la ANSI S.20.20 trova maggiore applicazione nel Nord America e Giappone; nella realizzzione di entrambe si è considerato che il loro utilizzo potesse essere recepito da parte di aziende di qualunque dimensione.
I criteri tipici delle attività di mantenimento debbono essere stabiliti da procedure interne le quali debbono necessariamente fare riferimento a normative esterne attive.
Le procedure ESD infatti oltre a contenere indicazioni verso le caratteristiche elettriche – fisiche – meccaniche dei prodotti impiegati per la protezione debbono contenere anche i criteri di base per il mantenimento dell’ area / processo quali le cadenze del monitoraggio sulle dotazioni ed i criteri con cui sono condotte le verifiche ispettive inclusa l’ eventuale gestione delle azioni correttive a fronte di problemi emersi.
Piani Di Mantenimento
1) Monitoraggio
L’ attività di monitoraggio viene tipicamente eseguita dagli utilizzatori o da personale diretto (che riferisce alla linea manageriale dei reparti di produzione). Di seguito (tab b) sono i sistemi di protezione normalmente verificati – tracciati, la periodicità ed il responsabile della attività.
# | Elemento | Periodicità controllo | Responsabile |
---|---|---|---|
1 | Bracciale | Giornaliera | utilizzatore |
2 | Calzature | Giornaliera | utilizzatore |
3 | Parametri ambientali | Giornaliera | Focal Point di reparto |
4 | Superfici di lavoro | Mensile | Focal Point di reparto |
5 | Ionizzatori | Mensile | Focal Point di reparto |
Tab. b: attività di monitoraggio su dotazione EPA
2) Veriche ispettive - Gestione azioni correttive
Tali attività (vedi tab. c) debbono essere condotte-coordinate da un ente al di sopra delle parti (quality assurance) - e nel caso delle “self review” da un focal point ESD che non dovrebbe riferire direttamente alle linee di produzione.
Le attività di verifica ispettiva si basano pricipalmente su tre aree ben definite (ref. Guida CEI 101-1) che sono :
- Idoneità dei sistemi in uso (incluse analisi elettriche vs parametri principali) per accertare problemi di degradazione – design
- Comportamento (rispetto delle procedure di base da parte del personale)
- Aspetti organizzativi (esecuzione – registrazione controlli – pianificazione etc.)
La parte inerente l’ idoneità dei sistemi in uso (misure elettriche – performance) richiede strumentazioni molto affidabili e personale specializzato e per questa ragione molte aziende si affidano a laboratori esterni in grado di accertare l’ affidabilità dei processi e le operazioni critiche (applicazioni speciali – compatiblità tra i sistemi).
# | Elemento | Periodicità controllo | Responsabile |
---|---|---|---|
1 | Self review | Trimestrale | Focal Point di reparto |
2 | Independent Audit | Annuale - semestrale | Coordinatore ESD |
Tab. c : attività di verifica ispettiva di EPA
Di seguito sono elencate le principali deviazioni che vengono riscontrate in sede di verifica ispettiva:
# | ELEMENTO | TIPO PROBLEMA |
---|---|---|
1 | Superfici di lavoro | Open – rs >1*109 ohm |
2 | Carrelli | Open – rs >1*109 ohm |
3 | Pavimentazioni | Rg > 3.5*10 107 ohm – HBV >100 volt |
4 | Bracciali / calzari | Cavi interrotti – rg Rg > 3.5* 107 |
5 | Imballi | Degradati – Out spec – no shield |
6 | Ionizzatori | Decay time > 20 sec – elettrodi fuori servizion |
7 | Vestaglie | Degradate – PtP >1*1011 ohm - ESD field > 2000 volt |
8 | Safe work station / equipments | ESD field > 2000 volt |
9 | Isolanti | Out safe distance – no ioniser – bad handling |
10 | Formazione | Non adeguata – no 100% people – non erogata |
11 | SAFE WOK STATION | Sistemi di protezione non idonei/poor/bad design |
12 | EXECUTION | Utilizzo non idoneo dei sistemi di protezione |
Conclusioni
Le attività di maintenance sono un elemento decisamente critico e fondamentale affinchè la gestione della statica sia opportuna nell’ ambito nei processi produttivi: la cattiva gestione delle attività di maintenance introduce problemi molto seri sia nei processi elettronici che in tutti quelli esposti al fenomeno ESD.
Anche la scelta più sofisticata e costosa può essere inibità attraverso operazioni di mantenimento improprie o la mancanza di attività di monitoraggio nei termini necessari che sono indicati da norme vigenti e/o tipologia soluzioni adottate.
Per soddisfare i requisiti richiesti è fondamentale predisporre un programma di controllo in grado di limitare al minimo le possibilità di errore e che coinvolga tutte le funzioni ed i reparti impattati direttamente ed indirettamente nella gestione della statica.
Riferimenti Bibliografici :
[1] EN 100015/1 - Protezione dei componenti sensibili a a cariche elettrostatiche ESDs Parte 1 requisiti generali - 1991
[2] IEC 61340-5-1 Protection of electronic devices from electrostatic phenomena - General requirements -1998
[3] ESD: ANSI/ESD S20.20. – for the development of an Electrostatic Disharge Control Program for - Protection of electrical and electronic …………. - 1999
[4] Evaluation of Surface Resistivity meas. on ESD protective Mats - IOP Electrostatic 95 International Conference - York University. G. Reina - P. Malinverni 1995.
[5] ESD: Triboelettricità vs Resistenza la correlazione non è sistematica - IV Giornata Nazionale di studio sulle problematiche ESD – G. Coletti – G. Reina - Settembre 2001
[6] Mantenere nel tempo l’ efficienza delle aree EPA - V Giornata Nazionale di studio sulle problematiche ESD – E. Renier - Maggio 2003